How to service crankshaft.
Complete crankshaft servicing details.
Crankshaft Operation:
A revolving part mounted in the lower portion of the engine block.
That part of a reciprocating compressor on which the wobble plate or connecting rods are attached.
Setup to check crankshaft warpage.
The actual amount of crankshaft warpage is half the total indicated reading.
Exaggerated view of crankcase housing misalignment.
Evaluating alignment bow.
Preening a crankshaft to remove warpage.
Crankshaft endplay can be checked with a feeler gauge.
Crankshaft endplay can be checked with a pry bar and dial indicator.
Most engines use a main bearing that has thrust faces to limit endplay.
A typical crankshaft seal.
A crankshaft grinder. NOTE
Complete crankshaft servicing details.
Crankshaft Operation:
A revolving part mounted in the lower portion of the engine block.
That part of a reciprocating compressor on which the wobble plate or connecting rods are attached.
A worn crankshaft does not always require replacement. Depending on the severity of the damage and the material the crankshaft is constructed from, it may be reconditioned with no adverse affects. In addition, many crankshafts can be straightened. However, do not attempt repairs on a cracked crankshaft.
Crankshaft specifications can be found in the engine specification section of a service manual.
Checking for Warpage
- To check for crankshaft warpage, place the crankshaft into two V-blocks or between lathe pins so they support the end main bearing journals.
- Install a dial indicator on the middle main bearing journal with the plunger positioned in the three o'clock position on the journal.
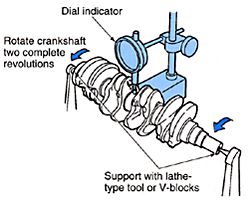
- Rotate the crankshaft one revolution while observing the dial indicator.
- The amount of crankshaft warpage is 50% of the total indicator reading (TIR).
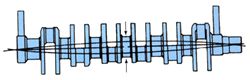
- Remember, any journal out-of-round will affect the TIR.
- If specifications are not available, a general rule is that TIR should not exceed half of the minimum bearing clearance specification.
- Record the indicator readings and mark the high spots on the journal.
- The highest of the run out readings indicates the point of the bend.
- Marking the points of highest run out on each journal provides a general plane of the bend.
- All of the marks will usually line up. If they do not, this indicates multiple bends in the shaft.
Checking Saddle Alignment
Below is an exaggerated illustration of crankcase housing bores that are out of alignment.
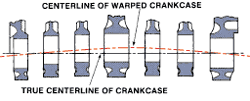
If the block is warped and its main bearing bores are out of alignment, the crankshaft will inflict heavy loads on one side of the main bearings. Engine blocks that are not severely warped can be repaired by an operation called line boring, a machining operation in which the main bearing housing bores are rebored to standard size and in perfect alignment. Badly warped blocks need to be replaced.
The alignment of the crankshaft saddle bore can be checked with a precisely ground arbor placed into the bearing bores.
- The arbor is rotated in the bores; the effort required to rotate it determines the alignment of the bores.
- If a proper arbor is not available, saddle alignment can be checked with a metal straightedge.
- Place the straightedge in the saddles as shown.
- Using a feeler gauge that is half the maximum specified oil clearance, try to slide the feeler under the straightedge.
- If this can be done at any saddle, the saddles are out of alignment and the block must be line-bored.
- Repeat this procedure at two other parallel positions in the saddles.
Out-of-roundness of the saddles can also be checked by bolting on the main bearing caps and checking each bore with a dial bore gauge or an out-of-roundness indicator.
Checking Straightness
Straightening the crankshaft is done by relieving the stress tension built up in the shaft. The shaft is not bent back into alignment. Removing the stress within the crankshaft will automatically return it to its original shape. Stress is removed by striking the crankshaft in the direction of the bend.
WARNING- To evaluate the straightness of the crankshaft, the shaft should be supported by V-blocks positioned on the end main bearing journals.
- Position a dial indicator at the three o'clock position on the center main bearing journal.
- Set the indicator at 0 (zero) and turn the crankshaft through one complete rotation.
- The total deflection of the indicator, the amount greater than zero plus the amount less than zero, is the TIR.
- Bow is 50% of the TIR.
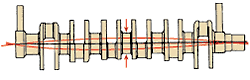
- Compare the bow of the crankshaft to the acceptable alignment/bow specifications.
- In most cases, if the crankshaft is warped, it is replaced.
If the crankshaft is to be straightened, this procedure must be done before any other machining operations are performed. there are two methods for straightening the crankshaft: peening and using straightening presses. both methods work on forged and cast shafts; however, pressing cast shafts requires extra caution. only serious engine rebuilding shops will do this procedure.
To use the peening method:
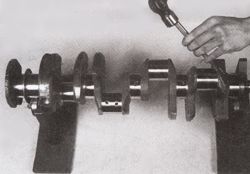
- Use a hammer and rounded bronze chisel with its end dressed to fit the fillet radius of the rod journals are used for peening.
- Striking the journal in this location prevents damage to the bearing surface.
- The chisel is struck with a hard, sharp blow from the hammer.
To use the pressing method:
- The crankshaft straightening press applies hydraulic pressure to the bend.
- A dial indicator is attached to the journal to indicate the amount of overbend being applied.
- At this time, the chisel and hammer are used to strike the fillet radius of the bent journal in the direction of the bend.
- This is done to relieve stress in the shaft.
Crankshaft Endplay
Crankshaft endplay can be measured with a feeler gauge by prying the crankshaft rearward and measuring the clearance between the thrust bearing flange and a machined surface on the crankshaft.
- Insert the feeler gauge at several locations around the rear thrust bearing face.
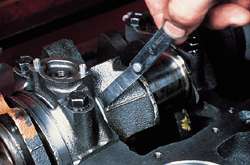
- Or position a dial indicator so that the fore and aft movement of the crankshaft can be measured.

- If the endplay is less than or greater than the specified limits, the main bearing with the thrust surface must be exchanged for one with a thicker or thinner thrust surface.
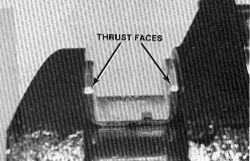
- If the engine has thrust washers or shims, thicker or thinner washers or shims must be used.
- Most engines require the installation of main bearing seals during the final installation of the crankshaft.
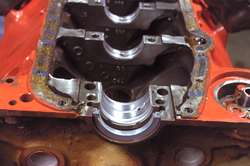
Crankshaft Timing
For the valves to open and close in correct relation to the position of the crankshaft, the camshaft must be timed to the crankshaft. This means the two shafts must be installed in such a way that the cam lobes open the valves at a precise time in relation to the position of the piston and crankshaft.
Regrinding the Crankshaft
A machine shop can regrind a crankshaft with a crankshaft grinder. Crankshafts are usually reground to 0.010", 0.020", or 0.030" undersize.
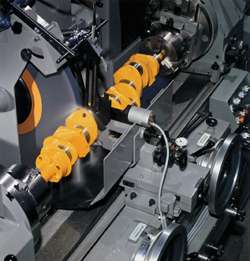
No comments:
Post a Comment